Calibration process is the method of adjusting an instrument or device to ensure its readings are accurate and precise. In simple terms, it’s like fine-tuning a machine to ensure it delivers correct results. The calibration process is vital across many industries, from electronics to medical equipment. For instance, when you calibrate a thermometer, you are making sure it shows the exact temperature, ensuring its accuracy when used for diagnosing health conditions..
Why Calibration Matters?
The importance of calibration lies in its ability to provide accurate readings that contribute to safety, compliance, and quality in various industries. Without proper calibration, even the most sophisticated equipment can give misleading results, leading to significant errors. This can cause safety hazards in healthcare, manufacturing, and research. Hence, calibrating equipment helps avoid costly errors and ensures that results remain reliable, preventing potential failures in production or diagnosis.
Types of Calibration
Calibration can take different forms depending on the device and industry. The two main types are manual calibration and automated calibration. Manual calibration requires human intervention to adjust devices manually, while automated calibration uses technology to adjust instruments more efficiently. Another crucial factor is choosing between in-situ calibration (calibrating instruments in their operational environment) or sending them to a laboratory for calibration.
The Calibration Process
The calibration process involves several steps to ensure that measurements are accurate. First, you must prepare the instrument and ensure it’s properly set up. Then, using reference standards, adjustments are made to match the device with the standard values. Finally, the instrument’s performance is tested again to ensure accuracy. This process can vary depending on the type of instrument being calibrated, but the goal is always to ensure precision and consistency.
Importance, Applications, and Practical Examples
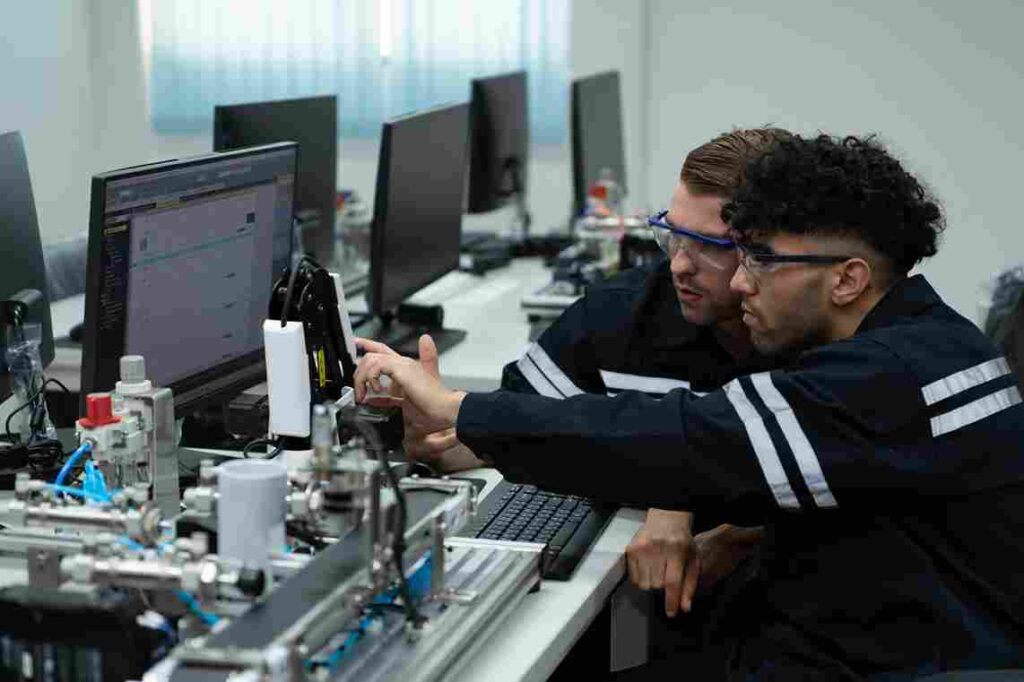
Why is Calibration Important?
Calibration plays a pivotal role in ensuring the accuracy and precision of measurements across different fields. Whether it’s for medical equipment, manufacturing processes, or scientific research, accurate readings are crucial. For example, if a thermometer isn’t calibrated properly, it can give incorrect readings, leading to inaccurate diagnoses. Similarly, in electronics, uncalibrated instruments could result in faulty production, affecting product quality and safety. Calibration ensures the reliability of these devices, which in turn helps avoid costly errors and even accidents.
Moreover, calibration is essential for meeting industry standards and regulations. Many industries require precise calibration to comply with local and international guidelines. Without calibration, industries risk facing legal issues and compromised product quality. This is why regular calibration is not just a technical necessity, but also a legal obligation in certain fields, such as healthcare and aerospace.
Applications of Calibration Process
Calibration is used in a wide array of industries, each requiring different tools and methods. In the electronic industry, multimeters, oscilloscopes, and other measuring tools need precise calibration to ensure they give accurate readings. In medical settings, devices like blood pressure monitors, thermometers, and pulse oximeters must be calibrated regularly to provide reliable health data.
For automotive calibration, car sensors, fuel gauges, and even GPS systems need periodic adjustments to maintain accuracy. Manufacturing also heavily relies on calibration to ensure that machinery operates within precision tolerances, thereby reducing the risk of defective products.
Practical Examples of Calibration
To understand the importance of calibration in everyday life, let’s consider a few common devices:
- Thermometers – Medical thermometers need to be calibrated to ensure the readings are accurate for proper diagnosis.
- Scales – Calibration of digital scales ensures that weight measurements are consistent, which is crucial in fields like shipping, healthcare, and retail.
- Torque Wrenches – A miscalibrated torque wrench can lead to improperly tightened bolts, which can cause failures in mechanical systems.
- Apple Watches and Fitness Devices – Calibrating these devices ensures accurate tracking of health metrics like steps and heart rate.
Challenges, Recalibration, and Final Thoughts
Common Mistakes in Calibration
Calibration can be a tricky process if not done correctly, and there are several mistakes that people make. One of the most common issues is skipping steps in the calibration process, which can lead to inaccurate results. For instance, missing out on reference standards or not performing the required checks can cause significant errors. Another mistake is using the wrong tools or equipment for calibration. Using a non-standard calibration device can lead to improper readings and unreliable results.
Environmental factors also play a major role in the calibration process. Changes in temperature, humidity, and even dust can affect the accuracy of measurements. For example, if a pressure gauge is calibrated in a controlled environment but later used in an outdoor setting, its readings may become inaccurate due to fluctuating weather conditions. To avoid these issues, it’s important to ensure that the calibration environment is consistent and controlled.
How Often Should Calibration Process Be Done?
The frequency of calibration depends on various factors such as the device being calibrated, the industry it’s used in, and its daily usage. Manufacturers usually provide guidelines for calibration frequency. For example, a thermometer used in a healthcare setting may need to be calibrated every 6 months, while equipment in a manufacturing plant might require monthly calibration to ensure high precision in production.
Industry-specific guidelines can also provide clarity on the right intervals for calibration. In sectors like aerospace and medical technology, calibration might need to happen more frequently to meet safety standards and regulations. Compliance with these guidelines ensures that devices remain accurate and reduce the risk of errors.
Recalibration: What, When, and Why?
Recalibration is the process of re-adjusting a device after it has been used over time. The need for recalibration arises when a device shows signs of drifting from its original calibration settings. This can happen for several reasons, including wear and tear, exposure to extreme conditions, or general usage over time. Devices like torque wrenches, scales, and blood pressure monitors often require recalibration after prolonged use.
The difference between calibration and recalibration lies in their purpose. Calibration sets the device to its ideal standard, while recalibration is the act of adjusting the device to restore its accuracy after it has deviated from the original calibration.
Conclusion
In conclusion, calibration is an essential process for ensuring that devices and equipment operate with the highest levels of accuracy and reliability. Whether it’s a thermometer, scale, or pressure gauge, regular calibration is vital to avoid errors and ensure consistent performance. Recalibration helps maintain the accuracy of devices over time, particularly those that experience heavy usage.
To achieve consistent, reliable results, it is crucial to follow the calibration process carefully, use appropriate tools, and maintain a controlled environment. By doing so, industries can meet safety standards, reduce errors, and save both time and money in the long run.
FAQs (Frequently Asked Questions)
- How do I know if my device needs recalibration?
If the device shows inconsistent readings or doesn’t match the expected measurements, it may need recalibration. - Can I calibrate my equipment myself?
While some basic calibrations can be done at home, professional calibration might be required for more complex devices to ensure optimal results. - What tools are needed for calibration?
Tools like calibration weights, reference standards, and calibration software are commonly used depending on the type of device being calibrated.